Overall Equipment Effectiveness
What is OEE?
Overall Equipment Effectiveness (OEE) is a key metric in industrial production that can be used to measure the productivity of machines and identify productivity losses in individual areas. In this article, we take a look at how OEE can be calculated and interpreted, using examples and introducing useful tools.
Definition
What is OEE?
OEE is the abbreviation for Overall Equipment Effectiveness and represents a key performance indicator relevant to industrial manufacturing. It is used to measure the productivity of a machine, production line or site.
The OEE metric is expressed in percent and made up of three main factors: Availability, Performance and Quality (also expressed in percent). In order to measure an OEE, these factors are first calculated and then multiplied.
The OEE and its components serve as an important controlling instrument in production management. When measured correctly, they are able to reveal where time or quality losses occur in the production process. This requires the necessary data to be defined and recorded and the resulting OEE values to be correctly visualized and interpreted.
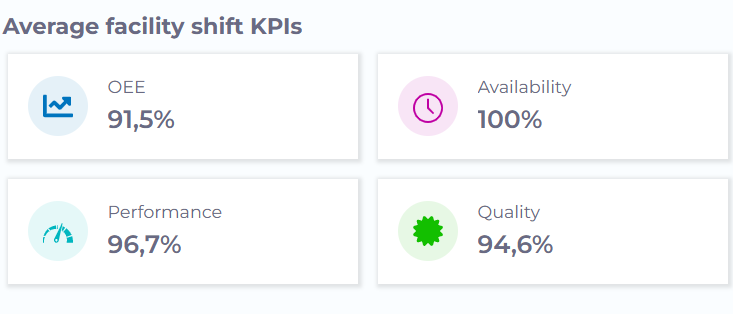
OEE visualization with manubes KPI Cards
Calculation
How is OEE calculated?
The Overall Equipment Effectiveness (OEE) is obtained using the following formula:
Availability x Performance x Quality
Below, we explain what these factors mean and how they are calculated.
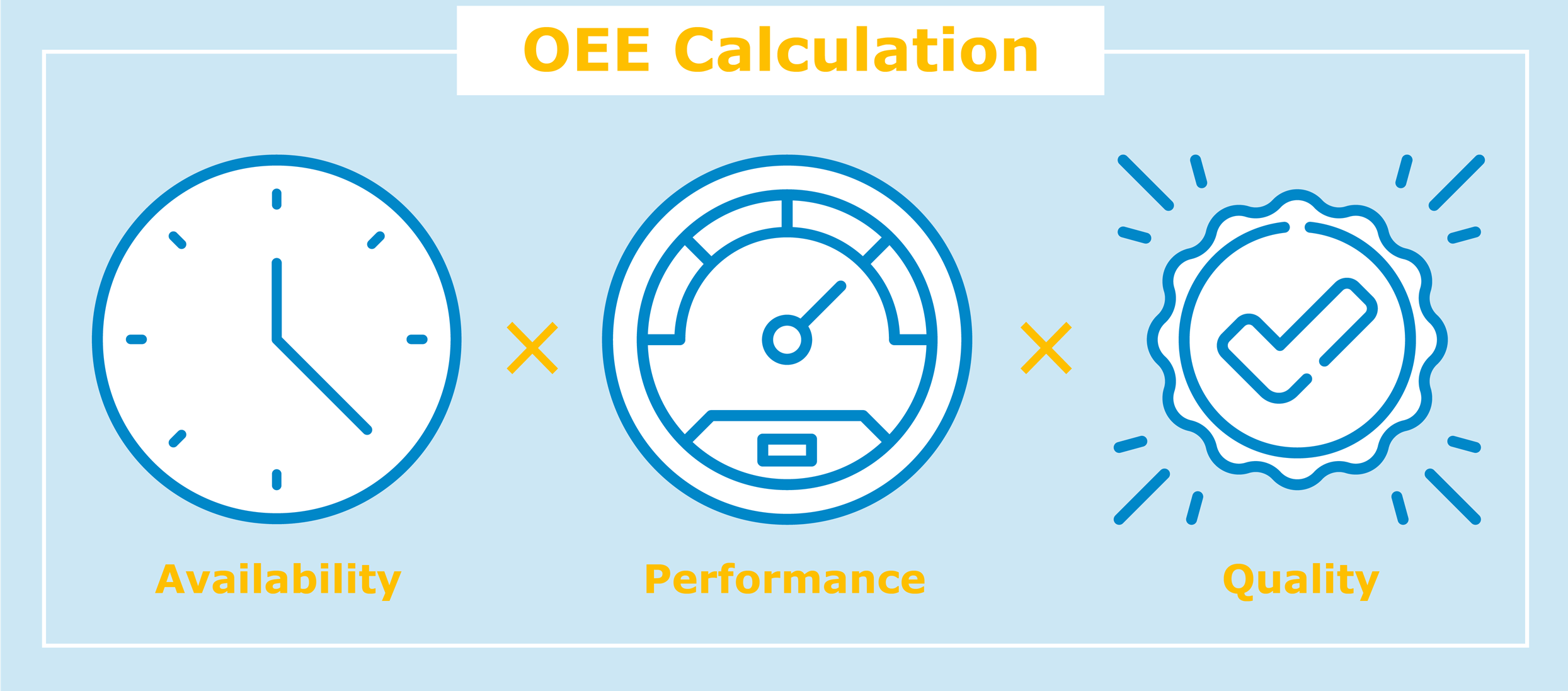
Availability
Availability is the ratio of the actual production time (run time) to the planned production time. Therefore, it is calculated by dividing the actual production time by the planned production time.
The availability component captures losses due to unplanned or unscheduled downtime (e.g. longer machine downtimes, missing operators, material bottlenecks) and changeover time.
Before calculating the OEE, it is important to determine how downtimes are incorporated into the calculation. Often, downtimes that last longer than one minute are recorded as Availability losses while shorter stops lower the Performance factor.
Example:
Planned production time: 480 minutes (shift duration) – 60 minutes (break time) = 420 minutes
Actual production time: 420 minutes (planned production time) – 33 minutes (downtimes and changeover time) = 387 minutes
Availability: 387 minutes (actual production time) / 420 minutes (planned production time) = 0,92 = 92%
Performance
Performance is the ratio of the number of goods produced to the maximum possible number of goods produced. This maximum quantity must be defined in advance, often using information provided by the manufacturer of a machine on the ideal cycle time (fastest possible time to produce one unit).
The performance factor is reduced by shorter stops and slower production due to errors, jams or similar.
The calculation of the performance factor becomes more complex if multiple products are produced on one machine.
Example:
Maximum production quantity: 20.000 units (Calculation: Ideal cycle time x Actual production time)
Actual production quantity: 18.000 units
Performance: 18.000 units / 20.000 units = 0,9 = 90%
Quality
Quality is the ratio of good products to the total number of products produced. Good products (good count) are all units that do not need to be discarded or reworked.
Losses in quality can occur due to inferior materials, machine wear or similar factors.
Example:
Number of goods produced: 18.000 units
Good count: 17.000 units
Quality: 17.000 units / 18.000 units = 0,94 = 94%
OEE
The OEE is calculated by multiplying the factors availability, performance and quality. With the example values used above, we obtain the following OEE:
Overall Equipment Effectiveness: 0,92 x 0,9 x 0,94 = 0,78 = 78%
For evalution purposes, not only the overall OEE ratio is relevant but also the sub-factors explained above. A typical OEE visualization presents the values for availability, performance, quality and OEE in one place.
If a correctly calculated OEE value exceeds 100%, it is likely that the actual production quantity exceeds the maximum production quantity (see Performance). In this case, the maximum production quantity must be adjusted in the calculation.
Practical implementation
How is OEE used in practice?
The OEE and its sub-factors can provide a quick overview over the productivity of existing systems and provide information on where (possibly avoidable) losses occur.
At the same time, it is important that the OEE is measured in the right place and interpreted correctly.
For which equipment should OEE be measured?
In practice, OEE should be measured at critical points within the production infrastructure, so-called „constraints“. These are usually machines or other systems that limit the possible production output by working at the slowest speed within a production line.
A focus on individual systems identified as constraints is most reasonable, as improving their OEE goes hand-in-hand with an actual increase in productivity. Of course, these constraints can shift over time, especially if a team is actively working on optimizing their OEE. Once a new machine is identified as a constraint, it is recommended to also calculate the OEE for that machine.
How can OEE be interpreted?
Once a value for the OEE of a system has been calculated, the next question is how to interpret it.
Even though it is theoretically possible to compare OEE values between plants, sites or industries, the indicator is primarily used to identify optimization potential. When calculating the values for availability, performance and quality, it becomes clear where the biggest losses occur and where corresponding measures should be planned.
A „blind“ focus on improving the OEE is not always sensible. For example, an increase in the quantity produced could lead to unnecessarily high stock levels if there is not enough demand.
The interpretation of the OEE factors depends, among other things, on the industry and the corporate strategy. In industries with complex manufacturing processes, higher reject rates and therefore a lower quality factor may be acceptable.
What is a good value for the OEE?
The question „What is a good OEE value?“ cannot be answered universally, as it is influenced by various factors such as changeover times or the type of materials used. In many cases, however, values between 80% and 90% are considered very good.
The comparability of OEE values between several machines and sites should at least be critically questioned, as different products may be manufactured and the production conditions may be different. For example, a production line that produces several different products will in many cases show availability losses due to changeover times.
What are the advantages of calculating OEE?
The greatest benefit of Overall Equipment Effectiveness lies in its ability to identify the sources of productivity losses. It therefore not only supports long-term optimization, but also enables quick reactions to sudden losses in availability, performance or quality (at least if OEE values are calculated and made available on a daily basis).

Digital production management in the cloud
With manubes, you are able to systematically automate production processes and visualize all areas of a production in real time.
OEE values can be calculated from machine data and user inputs, allowing everyone involved to gain valuable insights into the production processes.
The manubes platform offers worldwide access via web browser, easy operation and maximum security for production data.
Discover manubes!
Cloud-based production management with manubes: Our innovative platform offers specialized tools for connecting production systems, managing and visualizing production data and automating production processes. manubes users benefit from a powerful infrastructure, worldwide access and maximum security.