Industrial transformation is an ongoing process that can seem overwhelming at first glance.
Ath the same time, even small but well-implemented digitalization measures can lead to significant improvements in efficiency, quality and competitiveness for manufacturers.
In this article, we present five easy-to-implement applications for production that can deliver a major impact with minimal effort.
Your Partner for Digitalization Projects
For more than 30 years, we have been supporting industrial customers with digitalization and project optimization. Today, our products are used worldwide and in a multitude of industries.
With manubes, we are providing a platform that allows manufacturers to develop custom solutions for various environments and use cases. Contact us for an individual consultation and learn how manubes can optimize your production.
1. Digitized machine setup
Setting up machines is a critical phase in the production process – and unfortunately also a source of many potential errors.
Things can become especially problematic when operators have to manually enter sensitive parameters such as the expiration date or width settings for cutting blades. A simple typo is enough to render entire batches unusable.
Digitizing this process offers a simple solution: By reading the relevant parameters directly from the ERP order data and automatically transferring them to the machine, the human error factor is virtually eliminated. This not only ensures consistently high quality but also directly saves money by drastically reducing waste.
2. Material inspections prior to starting production
In the hustle and bustle of daily production, mistakes happen quickly: The wrong material or incorrect packaging finds its way into the manufacturing process – often with serious and costly consequences.
A simple yet highly effective solution is digital material inspection. Before production begins, the material is scanned. Only when the scan is successful and all requirements are met does the system send a release signal to the machine. And only then does production start.
This intelligent process ensures that only properly verified materials are processed. Defective production runs, time-consuming rework or even complete batches of scrap become things of the past. Quality increases, while costs and resources are simultaneously conserved.
Learn how manubes enables material verification via Barcode or QR code scan.
3. Automated creation and distribution of production reports
Production reports are the backbone of transparent manufacturing – yet manually creating them is often an unpopular and time-consuming task.
This is where digitalization comes into play: Modern systems capture production data directly from the machines in real-time and automatically generate a complete report. This report is available immediately after the end of production, without any need for manual input from the operator.
Even better: The report is automatically sent via email to the relevant decision-makers. This way, they receive up-to-date, reliable information as soon as production is completed and can respond quickly if needed – instead of waiting hours or even days for handwritten records that may contain errors or omissions.
Learn more about automated report generation with manubes.
4. Digital material flow release
In many manufacturing environments, delays frequently occur because material flows are released manually or without a structured process – a small error that can have major consequences.
A smart digital solution addresses this issue: After inspection, for example by the lab, a digital query is made to check product approval. The machine controllers automatically receive the information on whether a product has been approved for further processing. If it has, downstream processes such as storage, further processing, or special treatment can begin immediately without any manual intervention.
A solution like this can eliminate long waiting times, prevent material bottlenecks and avoid unnecessary downtime. The result: A smooth, uninterrupted material flow and significantly increased production efficiency.
5. Detailed visualization of machine status
In the past, machine conditions were often recorded only at specific moments – a quick glance at a number or status icon. But modern production processes demand greater transparency and proactive decision-making.
By continuously recording machine conditions over time and displaying them graphically in process curves, a more dynamic picture of overall machine behavior emerges.
Trends, deviations or gradual deteriorations become visible early – long before a sudden breakdown occurs. Production managers can compare curve progressions directly with current machine states, detect anomalies, and take targeted action.
This helps prevent looming quality issues or costly downtimes before they even arise. The level of clarity not only enhances operational security but also provides a solid foundation for ongoing process optimization.
Conclusion
The five easy-to-implement digitalization measures introduced above show that digital transformation in production doesn’t have to mean large-scale projects, high investments or complex overhauls. On the contrary – it’s often the small, targeted steps that have the greatest impact.
With focused adjustments, quality and efficiency can be significantly improved while minimizing downtime and waste. Those who seize these opportunities lay the foundation for sustainable, future-proof production and gain a true competitive edge.
With a flexible platform like manubes, such digitalization measures can be implemented easily, quickly and in a practical way. Thanks to simple device connectivity via OPC UA using the Edge Connector, there’s no need for costly new infrastructure. Existing machines and systems can be intelligently networked within a short time, making it possible to reap the benefits of digitization with minimal effort and investment. This makes the transition to more efficient, error-free production achievable for any company.
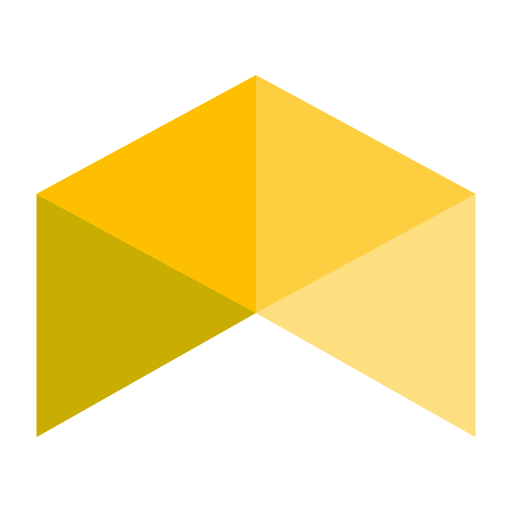
Production optimization with manubes
With manubes, manufacturers are able to rapidly develop their own solutions in areas such as production planning, process control and asset monitoring.
The innovative AI Assistant transforms production data into operative insights.
Recent Comments